Getting My Black Hawk Parts To Work
Wiki Article
The 2-Minute Rule for Black Hawk Parts
Table of ContentsWhat Does Black Hawk Parts Mean?Little Known Questions About Black Hawk Parts.The Of Black Hawk Parts4 Simple Techniques For Black Hawk Parts
KAMAN K-1200 K-Max synchropter In an alongside blades arrangement, 2 straight, counter-rotating rotors are placed side-by-side on a helicopter (or transverse rotorcraft). black hawk parts. The anti-torque result is supplied by the opposing rotation of the 2 major rotors. The side-by-side setup is just one of the possible flight configurations of a tilt-rotor aircraft, when the blades remain in the upright placement to supply upright lift.It is essential that parts are formed and ended up in an appropriate fashion. As a helicopter spare parts supper in the U.S.A., Jones Steel Products is below to form and end up helicopter components in a specific and prompt manner. Jones Steel Products has more than 95 years in the hydroforming sector, a procedure that we use for a selection of components in the aerospace as well as defense sectors.
As a helicopter parts provider, Jones Steel Products constantly invites outdoors organizations in for proper accreditations. These outdoors companies observe as well as validate the different procedures that we have on deal where we are making continuous advancements in composite manufacturing of helicopter components. ISO 9001:2015 without Style This accreditation connections to our quality monitoring system.
When it comes to being a relied on and valued helicopter parts manufacturer, making advancements in composite manufacturing of helicopter parts comes with the region. The procedures whereby we manufacture helicopter parts are always being boosted upon by our skilled group. Our team of engineers, designers, as well as metalworkers have been introducing our services because the 1920s.
About Black Hawk Parts
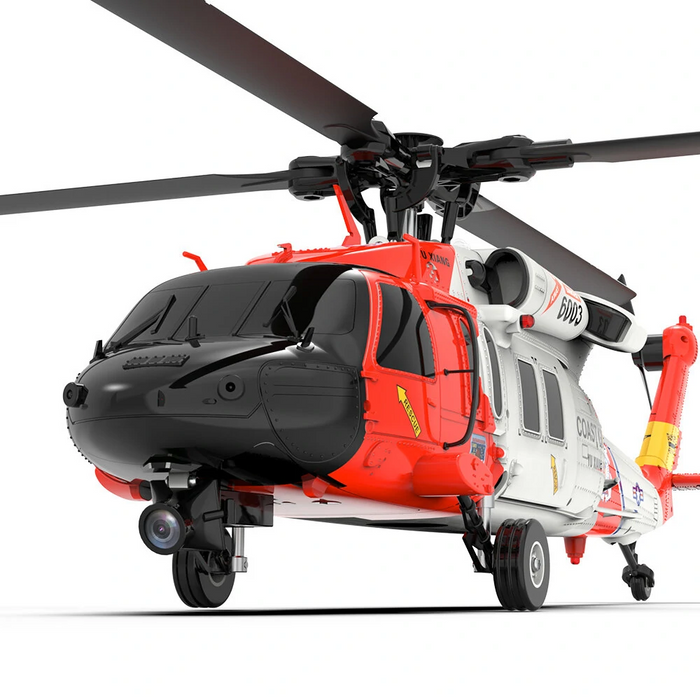
They can also aid you to recreate older helicopter components that stem from terminated runs all while maintaining in line with our high requirements of top quality and consistent manufacturing. Hydroforming, Rubber pad forming, Heat treating, Stretch developing As a leading helicopter components manufacturer, Jones Steel Products is happy to deal with customers in the aerospace, defense, and also aircraft sectors.

Helicopters are classified as rotating wing aircraft, and also their rotary wing is frequently described as the major blades or simply the rotor. Unlike the more typical fixed wing aircraft such as a sport biplane or an airplane, the helicopter can straight vertical liftoff and landing; it can also hover in a set setting.
The autogiro he subsequently created incorporated features of both the helicopter and also the plane, although it appeared like the last even more. The autogiro had a blades that functioned something like a windmill. As soon as propelled by cabbing on the ground, the blades can create additional lift; however, the autogiro was powered largely by a conventional aircraft engine.
Get This Report about Black Hawk Parts
To steer blog a helicopter, the pilot has to adjust the pitch of the blades, which can be established 3 means. In the cumulative system, the pitch of all the blades affixed to the rotor equals; Get the facts in the cyclic system, the pitch of each blade is made to fluctuate as the rotor rotates, and the 3rd system makes use of a mix of the very first two.A related problem happens because, as the helicopter moves on, the lift underneath the blades that enter the airstream initially is high, however that underneath the blades on the contrary side of the blades is reduced. The web result of these troubles is to undercut the helicopter. Commonly, the means of compensating for these unpredictable variations in lift as well as drag is to manufacture versatile blades attached to the blades by a joint.
Torque, an additional trouble connected with the physics of a rotating wing, causes the helicopter fuselage (cabin) to revolve in the opposite direction from the blades, specifically when the helicopter is moving at reduced rates or hovering. To offset this response, numerous helicopters make use of a tail blades, a subjected blade or ducted follower placed on completion of the tail boom commonly seen on these craft.
He experimented for greater than twenty years and also finally, in 1939, flew his very first flight in a craft called the VS 300. Tethered to the ground with long ropes, his craft flew no more than 50 feet off the ground on its very first numerous trips. Even after that, there were issues: the craft flew up, down, and laterally, but not forward.
How Black Hawk Parts can Save You Time, Stress, and Money.
His ideas were ultimately established right into the computer-numerical-control (CNC) maker device industry that has actually revolutionized modern-day manufacturing methods. 1 Each specific tubular component read here is cut by a tube cutting machine that can be promptly established to produce different, accurate lengths and defined batch quantities.For other than minor bends, tubes are full of molten sodium silicate that hardens and also removes kinking by causing the tube to bend as a strong bar. The so-called water glass is after that removed by positioning thebent tube in boiling water, which thaws the internal material. Tubes that must be curved to match fuselage contours is fitted over a stretch developing machine, which extends the steel to an exactly contoured form.
The last process involves infusing wax or an alloy with a reduced melting factor into a mold and mildew or pass away. When the layout has been created, it is dipped in liquified metal as many times as required to achieve the thickness preferred. When the part has dried, it is warmed to make sure that the wax or alloy will melt as well as can be put out - black hawk parts.
Report this wiki page